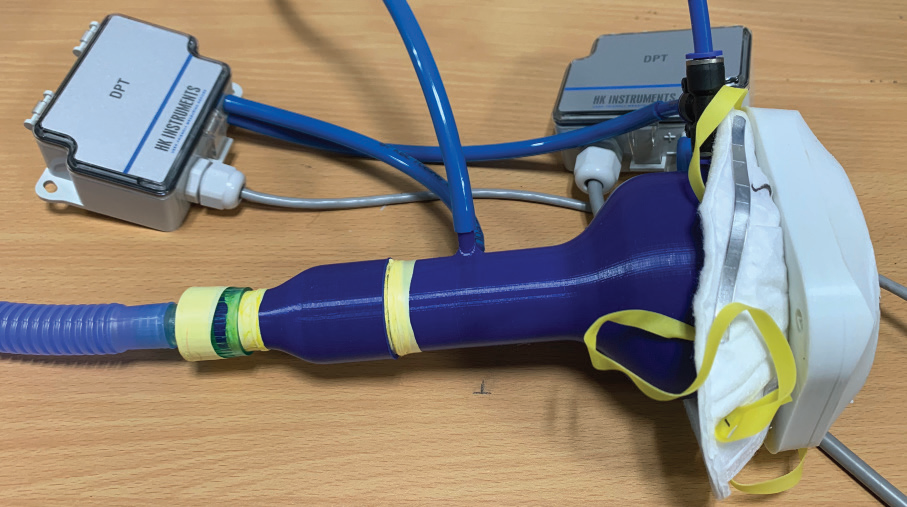
To address the acute shortage of N95 masks due to COVID-19, our team at the Centre for Nano Science and Engineering (CeNSE), in collaboration with Manipal Hospital and KAS Technologies, decided to set up a system to test whether it is safe for healthcare workers to reuse their N95 masks after decontamination. This setup is now being used to test the efficiency of all kinds of masks.
Masks are tested on various parameters, but we focused mainly on two aspects: particle filtration efficiency and breathing resistance. Particle filtration tests indicate how effectively the masks filter out particles of various sizes. N95 masks, for instance, are expected to filter out 95% of particles of sizes 0.3 micron and above.
Breathing resistance, on the other hand, provides a measure of how easy it is to breathe through the masks. There are various standards that specify the acceptable breathing resistance of masks at different flow rates.
When we started in April, the nationwide lockdown made it extremely difficult to source equipment or parts. Using components and sensors that were readily available in CeNSE, we were able to set up a system to carry out the particle filtration test and the breathing resistance tests at different flow rates. We used a household vacuum cleaner, pressure sensors fabricated and packaged at CeNSE as well as some commercial ones, and a commercial particle counter readily available in the National Nano Fabrication facility. The rest of the components, including flow restrictors and components to fix the masks onto the setup, were 3D printed.
With this system, we have been able to help multiple faculty members from IISc who are keen on making materials for N95 masks, doctors with ideas to develop powered air-purifying respirators, and vendors who wanted to test imported N95 masks. Some indigenous N95 mask manufactures also got their masks tested with our system before sending it out for certification.