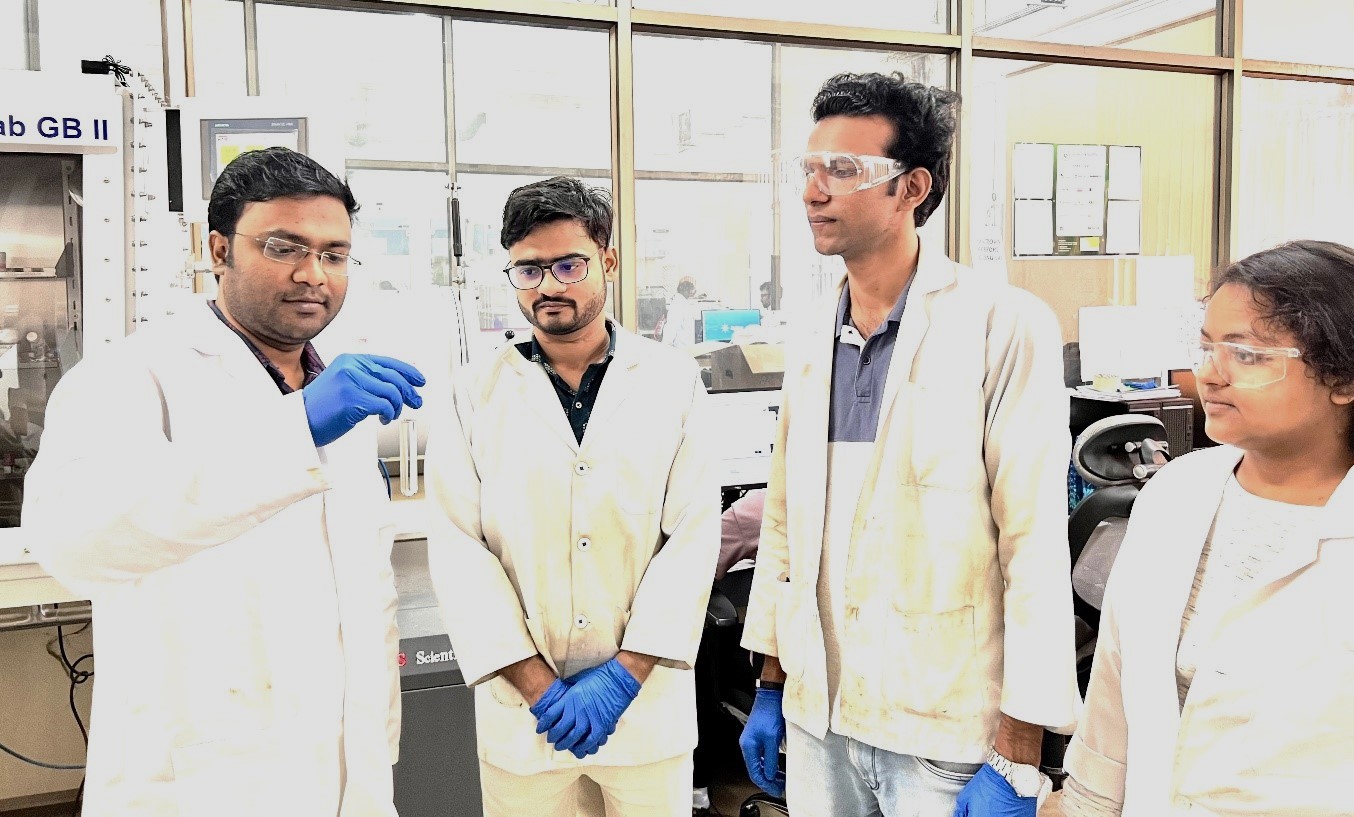
Industries and chemical labs synthesise a wide variety of organic molecules every day. Most of these chemical reactions happen in the liquid phase to allow the substrates to interact easily. However, many substrates and catalysts are sensitive to water and undergo side reactions, yielding unwanted products. This forces synthetic chemists to use toxic organic solvents. More than 80% of the waste generated in chemical processes is derived from such solvents – and not all of it is disposed of properly.
A team of researchers from the Department of Inorganic and Physical Chemistry (IPC), Indian Institute of Science (IISc) has now come up with a solution. They have synthesised a surfactant from agricultural waste to help catalyse industrially relevant reactions in water instead of organic solvents, through a process called micellar catalysis. The study was published in ACS Sustainable Chemistry & Engineering.
The surfactant they designed, called CNSL-1000-M, is derived from cashew nut shell liquid (CNSL), an agricultural waste product generated during the roasting of cashews to separate the kernels. “Since we were aiming for the replacement of organic solvents, we felt that the substitute must be bio-based,” explains Pritesh Keshari, first author and PhD student at IPC. India is the second largest producer of cashew nuts in the world, hence the raw material is easy and inexpensive to source.
Surfactants are molecules that have a water-loving (hydrophilic) as well as a water-repelling (hydrophobic) component. The researchers combined cardanol, a hydrophobic compound found in CNSL, with m-PEG, a hydrophilic polymer, to create their surfactant. When added to water, the surfactant molecules rapidly self-assemble to form small, spherical structures called micelles. The hydrophobic parts of the surfactant turn inwards, away from the water outside, forming a water-free pocket. Substrates and catalysts like nickel complexes, which are normally sensitive to water, can move inside these micelle pockets and remain protected.
“Suppose you dip a football in a pond or sea. As long as the football doesn’t leak, it remains floating with no water entering inside the ball,” explains Susanta Hazra, Assistant Professor at IPC and corresponding author of the study. “We use the same analogy for micellar catalysis. When the substrate goes inside the micelle, it separates itself and the reaction product from the bulk water – and that’s where the chemistry happens.” This micellar catalysis mimics biological systems – many natural enzymes have a hydrophobic pocket much like the one in micelles.
The team used their surfactant to catalyse the formation of carbon-phosphorus bonds, an industrially important step used to make many compounds including the anticancer agent Brigatinib and organic LEDs. CNSL-1000-M led to 80% higher product yields in water compared to reactions carried out in organic solvents. Compared to existing surfactants, the new surfactant also gave 30% higher yields for reactions carried out in water. Using the surfactant can also help replace expensive catalysts like palladium with inexpensive nickel complexes, and facilitate reactions at lower temperatures.
The researchers are keen to work with industries to enable the transition from using toxic organic solvents to aqueous micellar technology as the sustainable and green alternative. “We hope to study micellar chemistry in more detail and use our technology at the industrial level,” says Hazra. “Rather than making new surfactants for various types of reactions, our target is to use the same surfactant as a general reaction medium for all possible reactions and chemical transformations, as that is better for sustainability.”