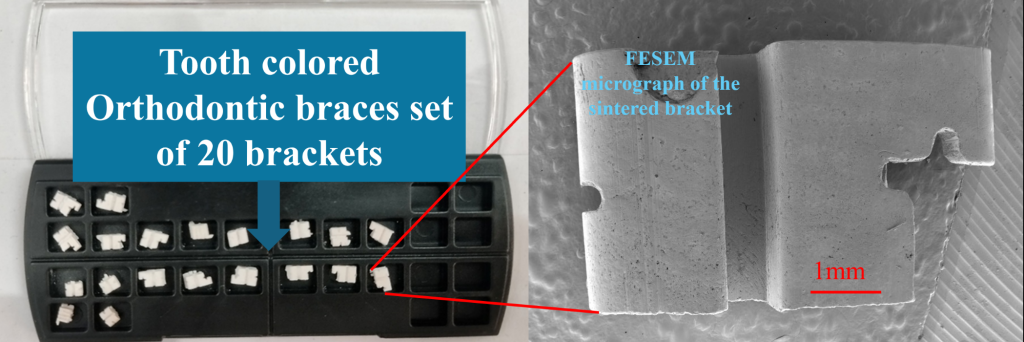
The healthcare industry uses several micro parts made of metals or ceramics. For example, ceramic brackets – small, square-shaped devices attached to teeth during orthodontic treatments – provide aesthetic appeal without significantly compromising the teeth’s function. While ceramics are inherently brittle, advancements in manufacturing have helped enhance their physical properties.
In a recent study, researchers from the Department of Materials Engineering, IISc, led by Prosenjit Das, have refined the development process for ceramic, orthodontic brackets using micro-ceramic injection moulding (μ-CIM) – a manufacturing technique that uses fine granules of alumina with a binder, which behaves like a temporary glue.
Using a special mould, the team successfully produced eight brackets in one shot which they then heated to remove the binder. In the final step, they baked the brackets at 1600°C. This final step fused the ceramic particles together, resulting in strong ceramic brackets that have a density very close to the ideal density value of alumina. This process allows for mass production of precise, high-quality brackets using fewer steps compared to older methods.
The researchers found that their polycrystalline alumina brackets were stronger and more durable than currently available commercial alumina brackets. The team also tested the ceramic brackets for cytotoxicity, and found that they are safe and compatible with biological tissues. Additionally, the study revealed that these brackets do not get stained by common beverages like tea and coffee, maintaining their original look even after prolonged exposure.
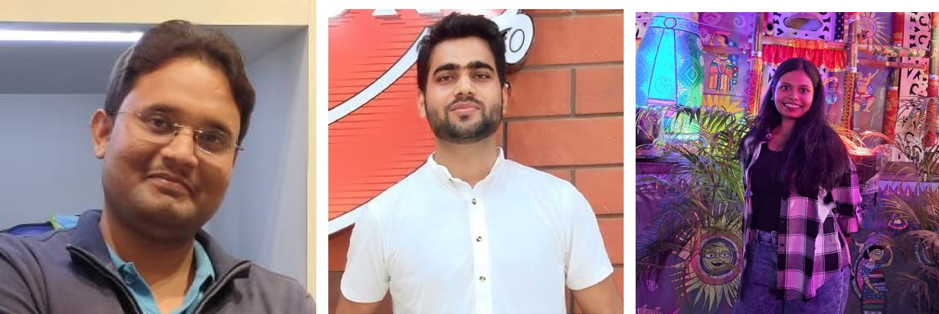