Abhik Choudhury’s lab investigates the mechanisms of microstructural evolution during materials processing
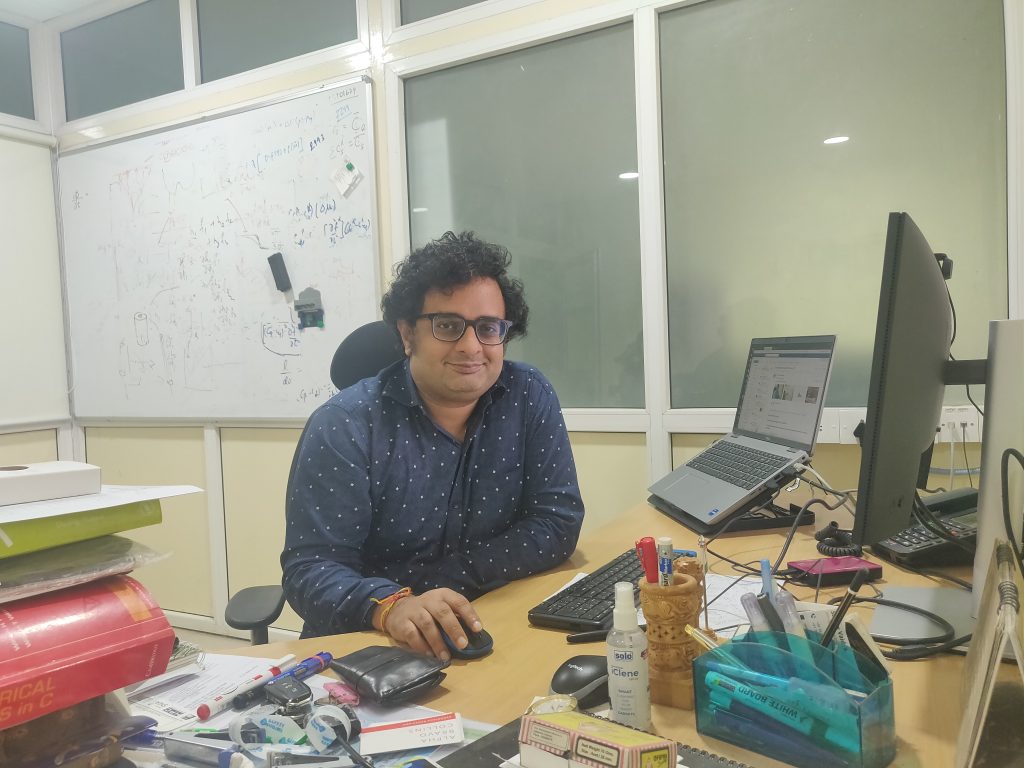
“Most of the problems of strategic importance in the country are materials-related and not so much design-related,” says Abhik Choudhury, Associate Professor at the Department of Materials Engineering.
Take the example of the jet engine, he explains. India has faced limited success in developing its own jet engine and therefore relies on importing it – like General Electric’s F414 engine – for combat aircraft such as the Tejas Mk2. The challenge lies not just in designing the engine itself, but also in ensuring that certain components like the high-pressure turbine blades possess the necessary strength to withstand extreme conditions encountered by the fighter aircraft. To achieve this strength, scientists need to go beyond choosing the right material – they need to fabricate materials with specific microstructures that remain defect-free even at the lowest molecular level. Addressing such challenges falls under the purview of a materials scientist like Abhik.
As a young student, Abhik was passionate about building machines and contemplated enrolling in a mechanical engineering programme for his Bachelor’s degree. However, following his board exams, he switched gears and opted to pursue a dual BTech-MTech degree in Metallurgical Engineering at IIT Madras. “It doesn’t really matter which field of engineering you have done because, at the end of the day, you cannot solve any problem of importance if you’re just there in that field [alone]. You have to appreciate problems going on in different fields, assimilate them and then collaborate to arrive at a solution,” he suggests. After IIT Madras, he went on to pursue a PhD at the University of Karlsruhe in Germany. During this time, Abhik says, his understanding and appreciation of material science grew even stronger.
At IISc, Abhik heads the Materials Modelling Group in the Department of Materials Engineering. The group focuses on developing materials called single crystals, which have a continuous and uninterrupted microstructure. Single crystals are known for their special properties and strengths, making them useful for various applications, including those required in jet engines. In order to produce single crystals, the team uses a technique called the Bridgman technique. It involves the gradual solidification of a melt or solution while maintaining a controlled temperature gradient. As a result of this gradient, the melt solidifies into a single crystal aligned with the direction of the gradient. The group is also exploring novel additive manufacturing-based methods to build single crystalline products.
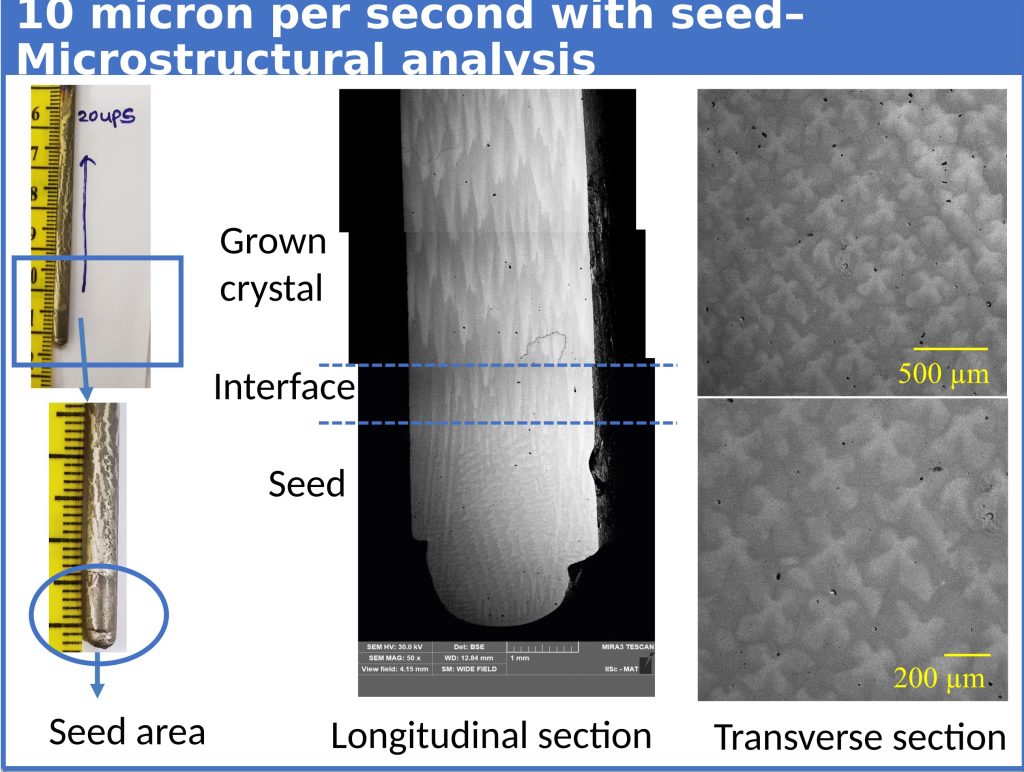
Abhik’s group also works on optimising existing approaches for single crystal generation. Specifically, they are focusing on enhancing the efficiency of investment casting, which is a process used to create single crystals of precise shapes and sizes. This optimisation involves modelling and fine-tuning all the processes involved in the production of single-crystal turbine blades. These processes include casting, homogenisation and heat treatment, and are inter-linked through the microstructural evolution history in each sub-process. Thus, a virtual workflow connecting the flow of information from one process to the next, such that the entire process chain can be optimised, is being developed by Abhik’s group in collaboration with professors from IITH and IITM.
Another exciting area that the team works on is predicting microstructural evolution and segregation during metal atomisation. This process involves melting metal and transforming it into liquid droplets, which ultimately settle as powders. The group seeks to thoroughly understand microstructure formation during atomisation. This can enable the production of powders with specific sizes, shapes, chemical composition, and purity. These metal powders are particularly valuable in sintering-based manufacturing, where they are compacted into desired shapes and then heated below their melting points. This controlled heating causes the particles in the powders to diffuse and rearrange, resulting in the formation of a solid structure. Such metals powders find widespread use in additive manufacturing (also called 3D printing), thermal spray coatings, catalysts, and sintered components used in the automotive, aerospace, and biomedical industries.
Abhik’s group is also keen on applying numerical analysis for energy-related projects, with a specific focus on clean coal utilisation. They work on identifying and developing materials suitable for boilers that operate under high pressure and high temperature conditions, where the choice of materials plays a critical role.
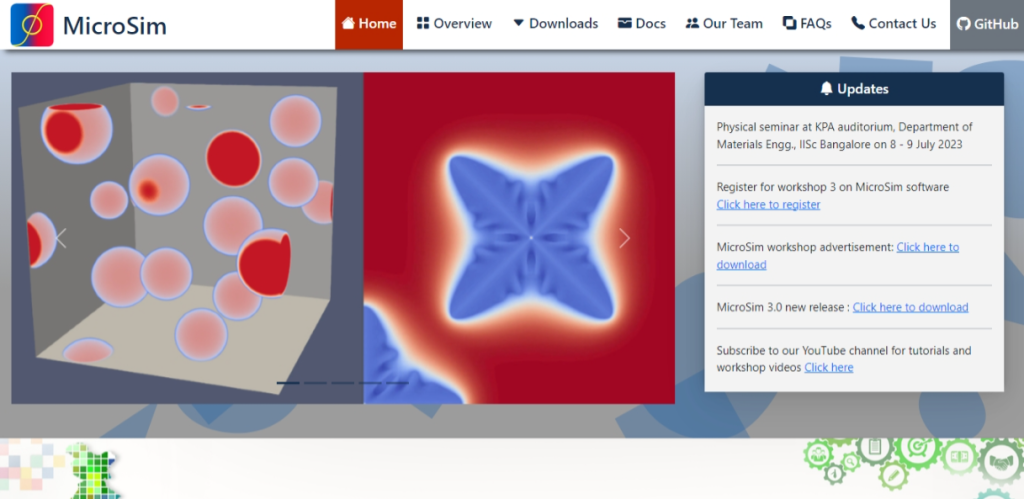
Apart from his own lab’s work, Abhik collaborates extensively with other researchers and industry partners. A notable outcome of one such multi-institutional partnership is the development of MicroSim (Microstructural Simulator), a user-friendly and open-source phase-field software package that can help researchers explore and optimise processes with desired properties. The software relies on a computational framework designed to simulate microstructural evolution occurring during typical materials processing. It uses mathematical equations to recreate various phases or states of a material and track how these change over time and under different conditions. For example, to model a casting process in which a metal solidifies, the user can feed details corresponding to the cooling rates and material properties into the software. Based on these, the tool can be used to simulate microstructural evolution and gives the user a clear visualisation of how the microstructure of the material changes during the entire casting process. Similarly, researchers can study and better understand phenomena such as solidification, precipitation, phase transitions, and the formation of microstructures using such simulations.
Abhik usually likes to begin his day practising yoga as a way to “centre his mind and body” before heading to the office. Besides guiding his students and his lab’s research, Abhik also dedicates a portion of his day to his own research on solving emerging problems in materials science, as they keep him sharp and attentive. “In my experience, being receptive to the ideas that students bring forth and appreciating them requires a state of alertness,” he says.
To his students, he often emphasises the importance of integrity and pursuing their passion. “Take a keen interest in whatever you are doing and do it sincerely. Results will come, but be honest, that’s the heart of it. Everything else [will] fall into place.”
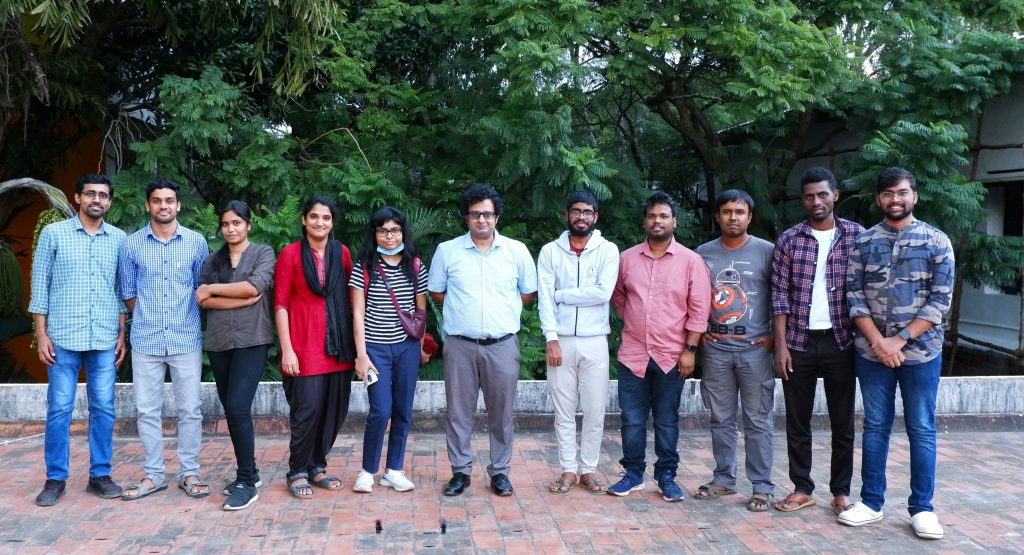