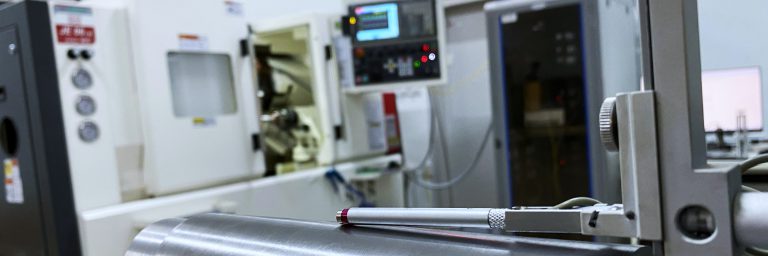
Machining has been used for hundreds of years to cut materials to desired shapes and sizes in order to make products ranging from small electronic circuit boards to huge engine components. Computer Numeric Control (CNC) machining employs computers to control the process and increase efficiency. CNC machining requires certain input parameters from human operators – NC code generated from 3D model of the product, feed rate, cutting speed and so on – which when fed to the machine produces the desired product.
The output of the process is judged by parameters called Key Performance Indicators (KPI) such as energy consumed during machining, surface roughness of the product, and so on. There is currently no way to accurately know which set of input parameters would result in which KPIs. The usual approach is to use physics-based models, but their calculations are generic. In a recent study, researchers from the Centre for Product Design and Manufacturing (CPDM), at IISc, led by B Gurumoorthy, have proposed a method to overcome this problem using machine learning (ML).
ML models are an ideal choice to solve this problem because they can learn from the vast amount of data available from past machining runs. Although ML models have been used before, in the current study, the researchers have integrated their model with the CNC machining interface for predicting KPIs. The insights obtained from this combination can help human operators better decide the input parameters needed to obtain the desired KPIs.
The model is also able to track and correct any deviations in planned values during the operation and instantly inform the human operators via a dashboard, which helps them immediately adjust the parameters. Such predictive models can greatly cut down production time and improve efficiency of CNC processes.
