A smart factory platform established at the Institute seeks to showcase how data-driven autonomous systems can transform traditional manufacturing to improve safety, quality and productivity
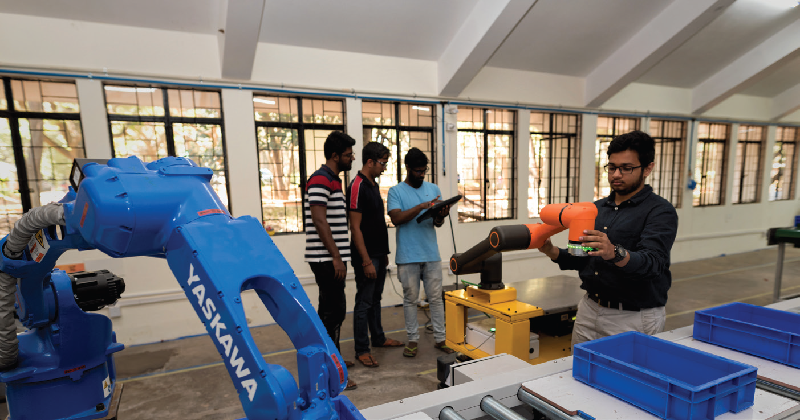
Advances in data analytics, machine learning and robotics are changing the way manufacturing works, leading many to believe that the world is on the brink of the fourth industrial revolution. Factories of the future will see a marked shift from automated machines that carry out programmed tasks to autonomous systems that can make intelligent decisions, according to Amaresh Chakrabarti, Chair of the Centre for Product Design and Manufacturing (CPDM).
A few years ago, Chakrabarti, along with colleagues Dibakar Sen and B Gurumoorthy, led the establishment of IISc’s – and India’s – first indigenous Smart Factory platform, a model factory that would incorporate sensing and data analytics, and provide a springboard for testing new ways to improve productivity, safety and sustainability, before they are adopted by industries. It was born out of a strategic partnership with The Boeing
Company, which provided seed funding.
“They wanted us to create what used to be called a network-enabled manufacturing facility, which is essentially a smart factory, but a very scaled-down version,” says Chakrabarti.
In a smart factory, data is collected at every level – from temperature sensors that track machine wear and tear to air quality sensors for noxious gases, and gesture sensors that evaluate workers’ postures. This data is then consolidated and analysed in near real-time using cutting-edge software and algorithms for faster decision-making. “The people, the products, the tools, the environment and the processes that are happening – all of them are connected,” says Chakrabarti.
In 2017, additional funding was committed by the Department of Heavy Industries (DHI), Government of India, to expand this project into a Common Engineering Facility Centre (CEFC) under the government’s Samarth Udyog Bharat 4.0 programme. Out of the Rs 25 crore funding sanctioned, Rs 20 crore comes from the government, while the remaining Rs 5 crore is raised from industry partnerships.
The CEFC’s mandate is multifold. The first is to operate as a demonstration centre to showcase what a smart factory would look like. Two types of platforms are being tested. One replicates an entirely automation-driven factory, with sensors, robots, and data analytics. Another focuses on incorporating some smart elements and technologies into a completely manual set-up, typical of Micro, Small and Medium Enterprises (MSMEs). For example, a sensor system using cameras and algorithms has been deployed in a small shoe manufacturing company to check materials for defects before they are manually assembled. This can substantially reduce material wastage and cost. “We are testing about 20 such platform technologies that can change the way individual companies work,” says Chakrabarti.
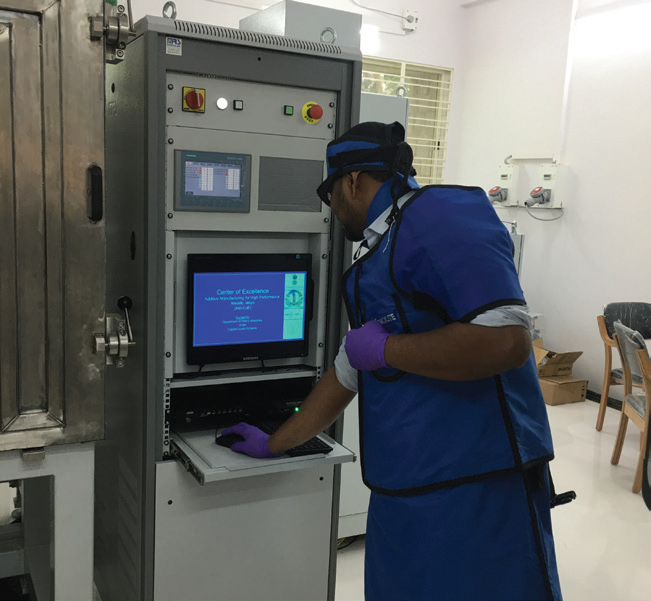
(Photo courtesy: Thulasi Raman)
The second goal is research on new manufacturing technologies. In 2019, with support from Wipro 3D and DHI, IISc researchers from various departments came together to develop the first prototype of an indigenous metal additive manufacturing machine, touted as a metal 3D printer. This machine uses a high power electron beam to melt metallic powders in a vacuum and build complex objects such as biomedical implants and aircraft components faster and more efficiently. New types of robots and cobots – machines that work alongside humans – are also being developed and tested. “The aim is to go beyond buying stuff and showing it off. We want to create our own capability in the country for all these technologies,” says Chakrabarti.
Another goal is to foster industry R&D. Several products and techniques are being developed with current partners Ashok Leyland, TCS, Toyota Kirloskar Motor, Faurecia and Yaskawa. These include smart wearables for worker safety, imitation learning approaches to train robot arms, smart imaging systems for surveillance, and real-time air quality monitoring systems. The facility also aims to nurture new and existing startups. Education and training is another goal of the centre. Several workshops, training programmes and visits have been organised for industry professionals, academic researchers, MSMEs and school children. An MTech degree programme in smart manufacturing and a PhD programme in advanced manufacturing have also been initiated at IISc.
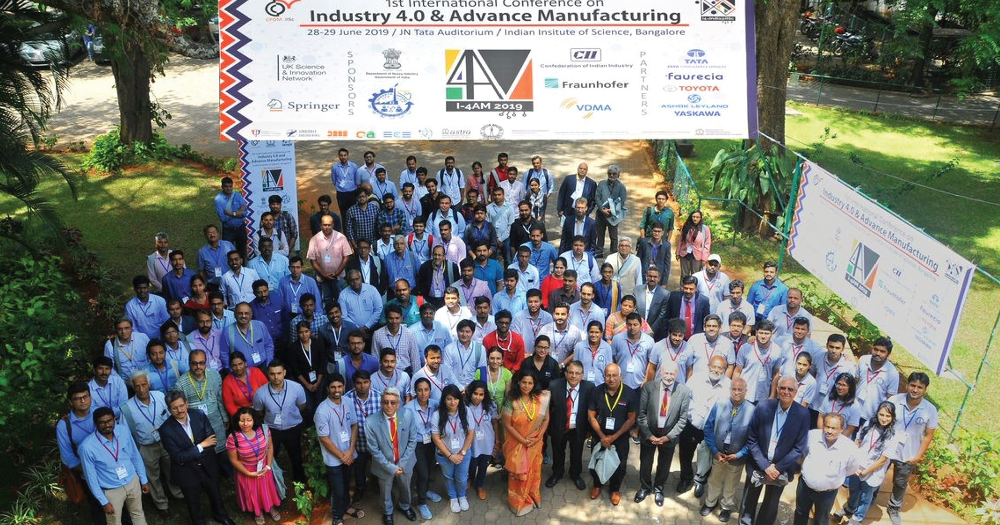