Research on biofuels and their integration into existing vehicles is picking up steam
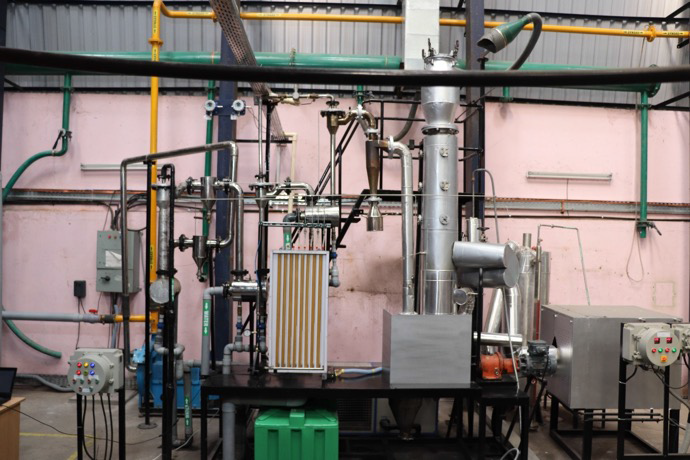
In a recent report, the Intergovernmental Panel on Climate Change (IPCC) declared that the adverse effects of climate change are far greater and vastly more disruptive to human life than previously understood. “Globally, heat and humidity will create conditions beyond human tolerance if emissions are not rapidly eliminated. India is among the places that will experience these intolerable conditions,” it states. Mumbai is at great risk of severe flooding and sea-level rise; Ahmedabad is an extreme example of an urban heat island; Chennai, Bhubaneshwar, Patna and Lucknow are approaching dangerous levels of heat and humidity.
These grim implications of climate change have prompted scientists to hunt for alternative technologies to produce and utilise greener forms of energy, which can curtail the rising concentration of greenhouse gases in the atmosphere.
While futuristic green hydrogen and fuel cell-powered automotive and aviation technologies are being pursued, a more immediate solution would be to develop simpler alternatives that can be readily integrated into existing systems and machines. One such alternative is liquid biofuels – typically alcohols and their derivatives from renewable and green sources. However, there are two main challenges in adopting liquid biofuels as alternatives to conventional fuels like petrol and diesel: producing them efficiently and in sufficient quantities, and adapting them for use in existing vehicles or machinery. Several researchers at IISc are currently working on addressing these challenges.
Dasappa S, Professor at the Centre for Sustainable Technologies (CST), has been working on converting biomass – typically wood and agriculture residue, which are renewable and carbon-neutral energy sources – into a combustible gaseous fuel called syngas, conventionally obtained from reforming natural gas. During the gasification process, biomass is progressively subjected to high temperatures in the presence of controlled reactants (primarily air or oxygen and steam). The complex chemical structure of wood is thermally decomposed and reduced to form syngas which is rich in H2, CO, CH4 and CO2.
Biomass gasification and the resulting fuel gas have various applications – from wood stoves at home to electricity generation through large-scale commercial gas engines. “The uniqueness of the fuel gas quality is its compatibility with the existing engines,” explains Dasappa. In the past two decades, over 100 biomass gasification units of various capacities (from kW to MW) have been commissioned in India and abroad. The technology transfer has saved 30 tons of fossil fuel per day, potentially avoiding the production of nearly 93 tons of CO2 per day, he says.
In addition to gas engines, recent developments have paved the way to utilise H2 and CO molecules in the syngas to generate liquid biofuels like kerosene and diesel using a cobalt-based catalyst developed and patented by the group. The flexibility that the technology offers to adjust the gas composition facilitates the generation of rich biofuels like high-purity hydrogen for fuel cell applications, as well as dimethyl ether and methanol.
Bio-methanol is widely recognised as a novel and promising fuel by technologists and policymakers. The government will soon mandate the use of petrol and diesel blends containing up to 15% methanol, reveals RV Ravikrishna, Professor in the Department of Mechanical Engineering. However, methanol’s properties and combustion characteristics differ from petrol and diesel, and different approaches are needed to adopt methanol in existing engines.
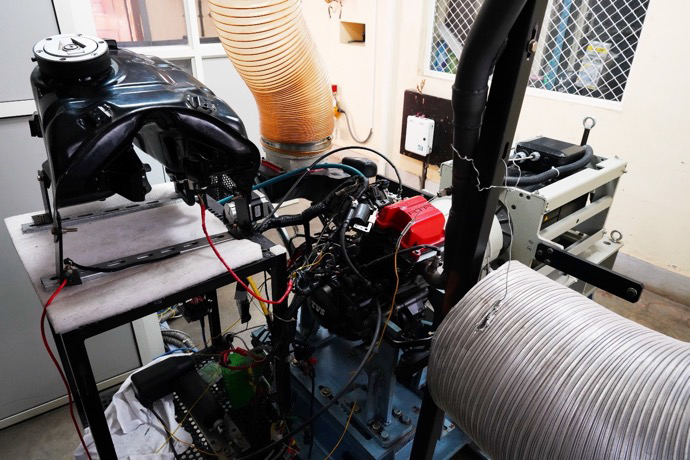
The energy generated on burning a unit mass of methanol is nearly half that of petrol, however, methanol burns faster than petrol, explains Ravikrishna. To address these challenges, he and his group have engineered fuel injection systems – based on an understanding of the fuel’s atomisation and its disintegration into droplets by electronically controlled injectors – and made changes to the engine control system to account for combustion properties of methanol. The technology is designed as a retrofit – it can be readily integrated into the existing engines. It has enabled the running of two-wheeler TVS engines and heavy-duty Ashok Leyland buses with 100% methanol, showing a 4-5% higher thermal efficiency than gasoline alone – a landmark achievement, according to Ravikrishna. “NITI Aayog has evinced keen interest in this work and has requested industry partners TVS Motors and Ashok Leyland to commercialise this technology at the earliest,” he adds.
“While methanol blends easily with petrol, when it comes to diesel, there’s a big challenge. It does not mix with diesel at all,” explains Ravikrishna. Efforts by his group on emulsions (mixtures of two or more immiscible liquids) have resulted in highly stable methanol-in-diesel macroemulsions containing up to 10% methanol, and methanol-dodecanol-diesel microemulsions containing even up to 30% methanol, which can be directly used in current engines. In addition, Ravikrishna’s lab is working on using hydrogen in engines as a step toward zero-carbon energy utilisation.
Just like the automotive industry, the global aviation industry aims to achieve net-zero carbon emissions by 2050.
D Sivakumar, Associate Professor in the Department of Aerospace Engineering, works in the niche area of using biofuels in the aviation sector. With advancements in technology, batteries could one day replace internal combustion engines in automobiles, but they don’t store enough energy to fuel a commercial airliner, says Sivakumar. In this context, biofuels emerge as one of the most promising alternatives in aviation. However, the aviation sector has its own set of challenges.
Unlike the automobile sector, modifications or retrofits to the aviation gas turbine could have significant implications for their performance and safety. Biofuels need to be chemically configured to reflect properties similar to conventional aviation fuels. Sivakumar and his collaborators have examined the properties of biofuels derived from plants (such as Jatropha and Camelina) and their flow properties when blended with conventional aviation fuels.
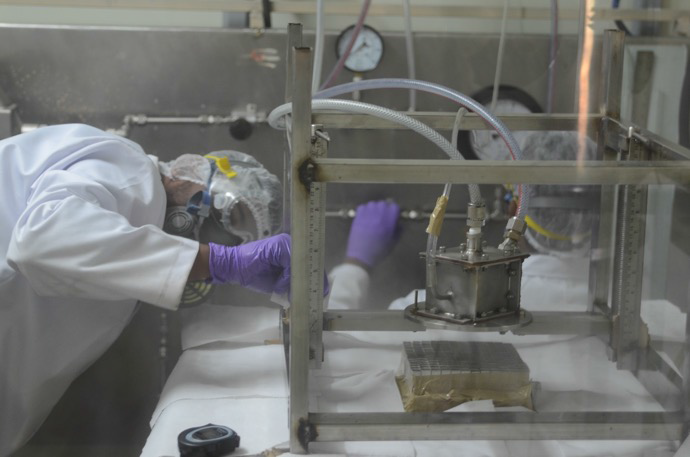
Such blended fuels (also called ‘drop-in’ fuels) need dedicated research on several topics to make them compliant with engine infrastructure and operation, explains Sivakumar. He and his group are working on understanding the atomisation and injection characteristics of biofuel blends. A promising result from their studies is the potential to use blends containing up to 70% biofuels as drop-in fuels.
Efforts to develop alternative fuels have been progressing rapidly in recent years. However, to bring these technologies and their benefits to the common person, collaborations between industry and academic institutions are crucial, remarks Sivakumar. “This is not a single laboratory’s work,” he says. Dasappa adds that policy decisions by the government will also determine the future of such alternative fuels.