New facilities at IISc open up exciting new possibilities in biology and medicine
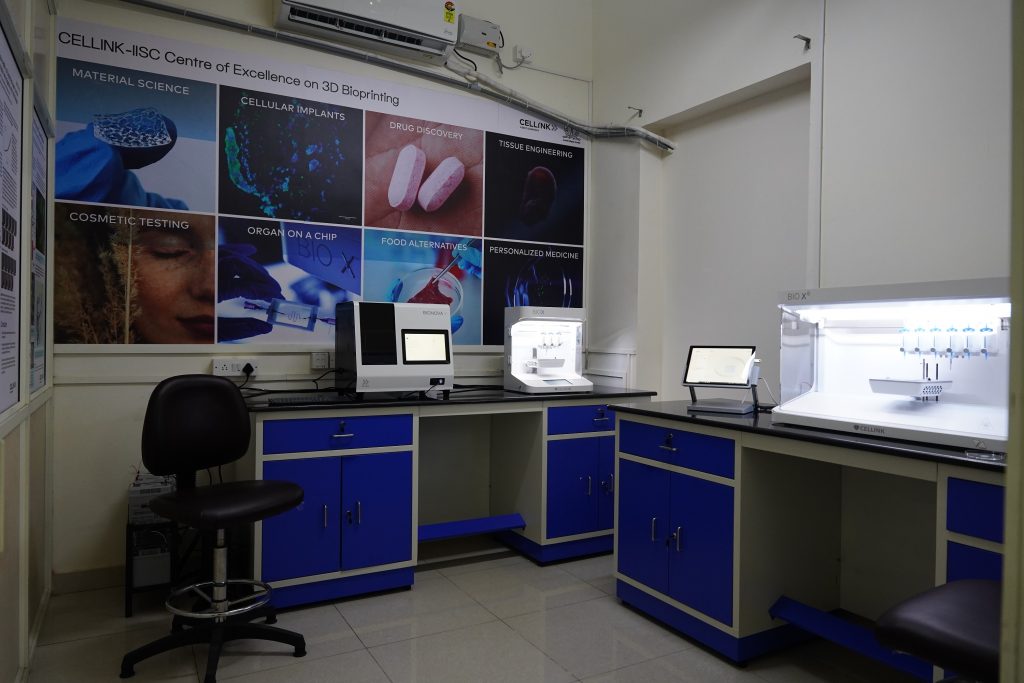
(Photo: KG Haridasan)
Imagine being able to print fabrics, toys, or even building materials. The idea is not so far-fetched with the advent of 3D printing. Now, imagine being able to print a heart, a lung, eyes and other organs too. This is also fast becoming a reality. For example, scientists at the National Institutes of Health (NIH) in the USA recently printed tissues of the eye, using an exciting new technology called 3D bioprinting, the next big thing in the world of 3D printing.
3D bioprinting goes one step beyond merely using 3D printed materials in biological applications. It involves using a mix of biologically functional materials like biomolecules and living cells to print living constructs such as tissues and eventually organs, which can then be used for medical research and applications.
Keeping pace with these developments, the Centre for BioSystems Science and Engineering (BSSE) at IISc, in collaboration with a company called CELLINK, recently launched a Centre of Excellence in 3D bioprinting. The purpose of this facility is to provide scientists at IISc and elsewhere access to cutting edge bioprinters that can help them test the printability of materials for biological research or create scaffolds (platforms on which cells and tissues can grow) and organoids (think mini organs made from stem cells) to perform experiments on.
Like regular printers, bioprinters also come in different shapes and forms. There are primarily three types – inkjet, microextrusion and laser-assisted bioprinters.
Microextrusion printers, the most common and affordable, work by continuously depositing small beads of the printing material on a substrate, controlled by a highly precise, robotic microextrusion head. In contrast, inkjet printers shoot out liquid droplets of the material which then solidify on the substrate. Laser-assisted printers use highly focused laser pulses – instead of robotic arms – to direct the biomaterial towards the substrate that is being printed on.
The Centre of Excellence in 3D bioprinting at BSSE houses high-end bioprinters like BIOX (extrusion printer with three printheads), BIOX6 (extrusion printer with six printheads) and BIONOVA X (a light based bioprinter).
The ‘ink’ for bioprinters can be biomolecules like DNA or proteins, or even live cells. The printing material may be specific to the tissues being printed, such as bone, cartilage and skin, and the printed product can then potentially be used for human organ transplantation. 3D bioprinted tissues and organs are also being increasingly used in research labs for solving real world problems, like testing the effects of new drugs.
“One of the things that we’re doing is to build organs on chips,” explains Narendra Dixit, Professor and Chair of BSSE. “We’re trying to build lungs on a chip or the peritoneum [lining of the abdomen] on a chip to study various elements associated with diseases.” According to him, 3D bioprinting can also potentially address ethical issues associated with animal drug testing. By creating reliable 3D organ mimics, one can test potential effects and side effects of drugs on them instead of on model organisms.
“3D printing and bioprinting, which is a subset of 3D printing, can be applied to a variety of materials, from metals to ceramics, to polymers,” says Kaushik Chatterjee, Associate Professor at BSSE. His team has successfully printed tissue mimics for drug testing and designed medical implants and orthopedic devices. Kaushik says, “3D printing allows you to have devices personalised for a person’s anatomy instead of doing a mass production of these pieces. We scan the area and make a 3D design of it in the software, and then we build it up layer by layer, personalising the part for a particular patient’s anatomy and possible defects.”
His lab is already doing this kind of work. They have, for example, 3D printed an adaptor which is a clamp-like device that can be customised to the hand of a patient with bone tumour, and can help a surgeon pinpoint where the tumour is, without having to guess, and remove it precisely. Currently, Kaushik’s team is collaborating with Sanjay Gandhi Hospital, Bangalore, to create personalised titanium implants to correct misaligned bones so that they can heal in the right orientation.
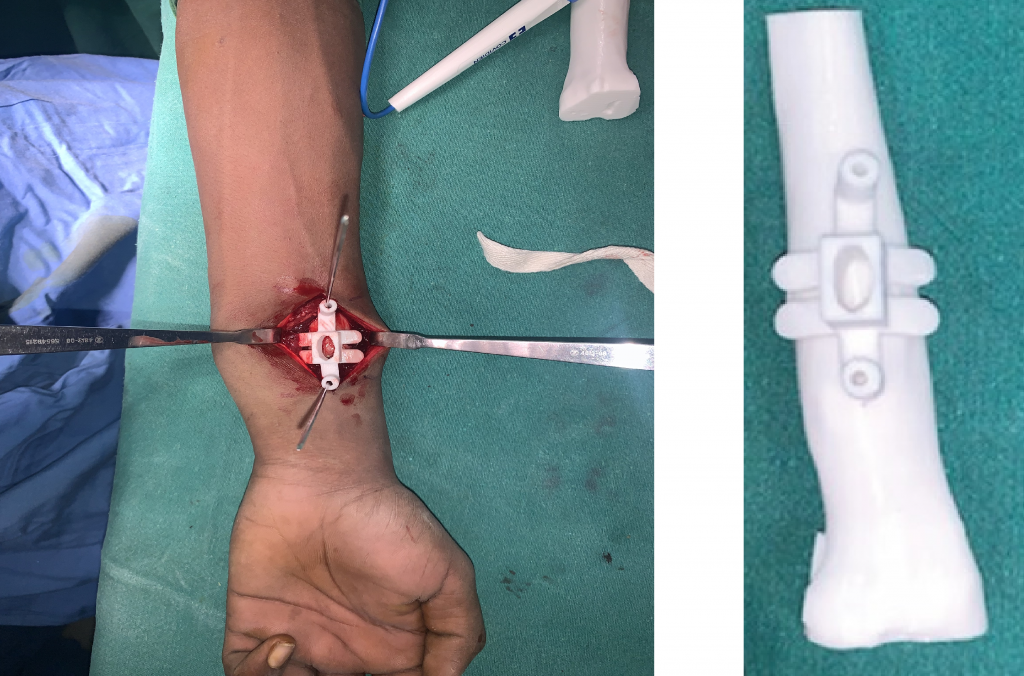
Right: Virtual model of the adaptor (Image: Saurabh Gupta)
“Another angle to bioprinting,” says Kaushik, “is mimicking what’s inside the body on the lab scale. What 3D bioprinting will allow us to do, is have different cell populations in different layers. Since you are depositing different gels layer by layer, you can have one cell population on your base layer, another in the next layer, and so on. This technique allows you to recreate the precise spatial distribution of cells inside the body.”
Beyond academic research, scientists at IISc are also pushing the soft barriers in terms of real-life implementation of elastomer printing. The Institute has a collaboration with a deep-tech startup called Prayasta.
Prayasta has developed a state-of-the-art 3D printer called SILIMAC. It can 3D print medical grade silicone to create breast implants for breast cancer survivors.
“For soft implants, silicone is the most appropriate material, being biocompatible. However, it was never designed for 3D printing. So, we developed the technology, or the machine, from scratch, which can 3D print silicone, especially the implant grade version of it,” explains Vikas Garg, Prayasta co-founder and CTO. “In fact, this will be the first soft tissue implant in the world that is directly 3D printed and not created using a 3D printed mould onto which the material is cast.”
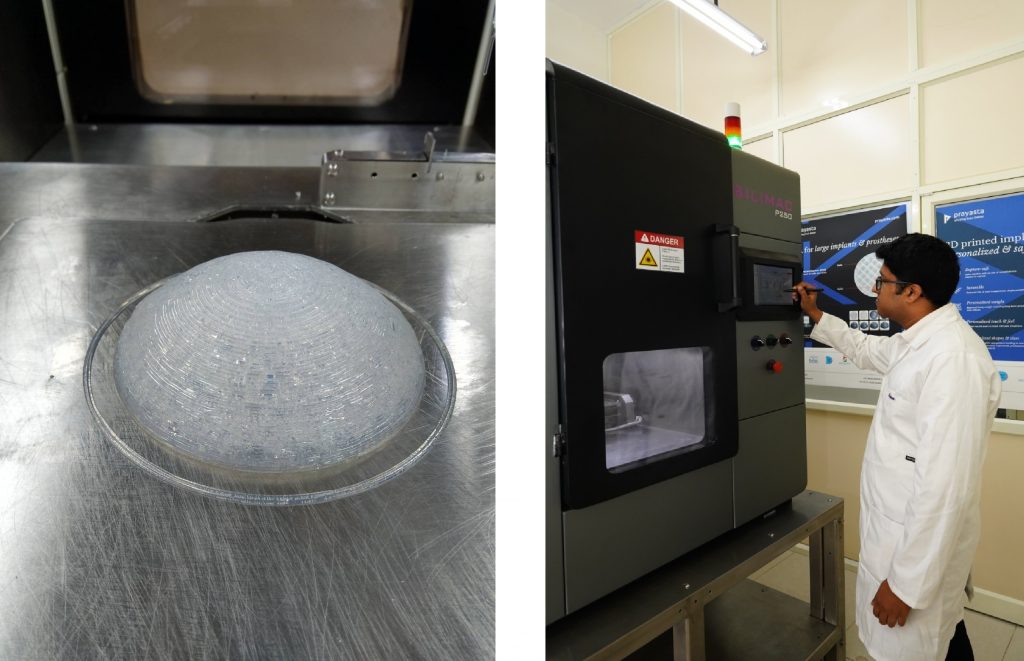
(Photos courtesy: Prayasta)
3D printing breast implants offers the advantage of personalisation in terms of weight, stiffness, shape and size. Such implants are devoid of any liquid, unlike the traditional saline implant which is prone to leakage after implantation. These 3D printed implants can also be sutured by a surgeon, which would prevent them from being malpositioned.
The collaboration with IISc, Vikas says, is a “win-win” situation. “While breast implant is in the pipeline, there are other tissues such as nose, chin, lip and ear, which may also require replacement [in facial reconstruction surgeries]. IISc provides the best environment for validating and developing novel devices.” IISc researchers aiming to develop novel materials can also use SILIMAC as a platform machine for testing their 3D printability, he adds.
BSSE’s 3D bioprinting facility, which opened its doors in December of 2022, also plans to organise outreach programmes for the wider research community in India. “The purpose of these programmes,” says Narendra, “is to, first of all, make people aware that such a technology really exists, and then to explain what the scope of this technology is. Mechanisms will be put in place, so that the machines are made accessible to the people outside IISc.”
Narendra adds, “[These] 3D bioprinters are definitely going to catalyse a lot of activity on campus.”