A new centre at IISc seeks to address the monumental problem of how to reduce coal’s environmental impact
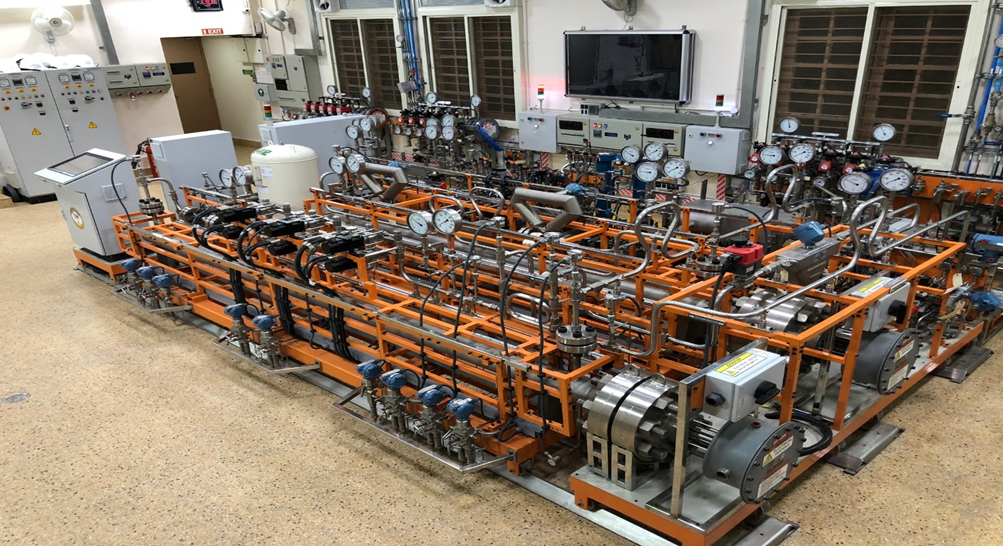
The climate change crisis has put the spotlight on fossil fuels, particularly coal, as a major source of environmental pollution. Coal is the most polluting fuel, but it continues to be widely used – it is India’s primary energy source – due to the large amount of power it can generate, its abundance and low cost.
The need of the hour is to make its use cleaner and more environment friendly. The National Centre for Clean Coal Research and Development (NCCCRD) at the Interdisciplinary Centre for Energy Research (ICER), IISc, established in 2019, aims to do just that. Funded by the Department of Science and Technology and led by IISc, it is a consortium of research groups from various institutions.
NCCCRD aims to develop technologies that increase the efficiency and reduce the environmental impact of coal as an industrial energy source, especially by reducing the carbon footprint of coal-based thermal power plants.
Thermal power plants burn fuels like coal to produce heat. This heat is carried by steam to turbines which rotate rapidly and produce electricity through a generator. Researchers at NCCCRD are exploring ultra-supercritical steam and supercritical carbon dioxide as alternatives to steam. Supercritical CO2 is a fluid state of CO2 above its critical temperature of 37°C and critical pressure of 72.8 atm. It has the properties of both liquid and gaseous states – it can expand to fill compartments like a gas, but is also dense like a liquid. Similarly, ultra-supercritical steam is the state of steam above its critical temperature and pressure, where it has the properties of both water and water vapour.
Both Advanced Ultra-Supercritical (AUSC) steam and supercritical CO2 plants would work at higher temperatures and pressures, which leads to a higher energy conversion efficiency. Therefore, more electricity will be produced for a smaller amount of fuel, reducing coal consumption.
Pradip Dutta, Professor at the Department of Mechanical Engineering and the Principal Investigator (PI) of NCCCRD, says, “We had previously set up a laboratory-scale supercritical CO2 Brayton test loop facility as a part of an Indo-US collaboration for solar thermal power plants in 2012, but it was limited to research at the systems level. Currently, we are developing components like special heat exchangers and turbomachinery that can operate at high temperatures and pressures for the supercritical CO2 based power plants.”
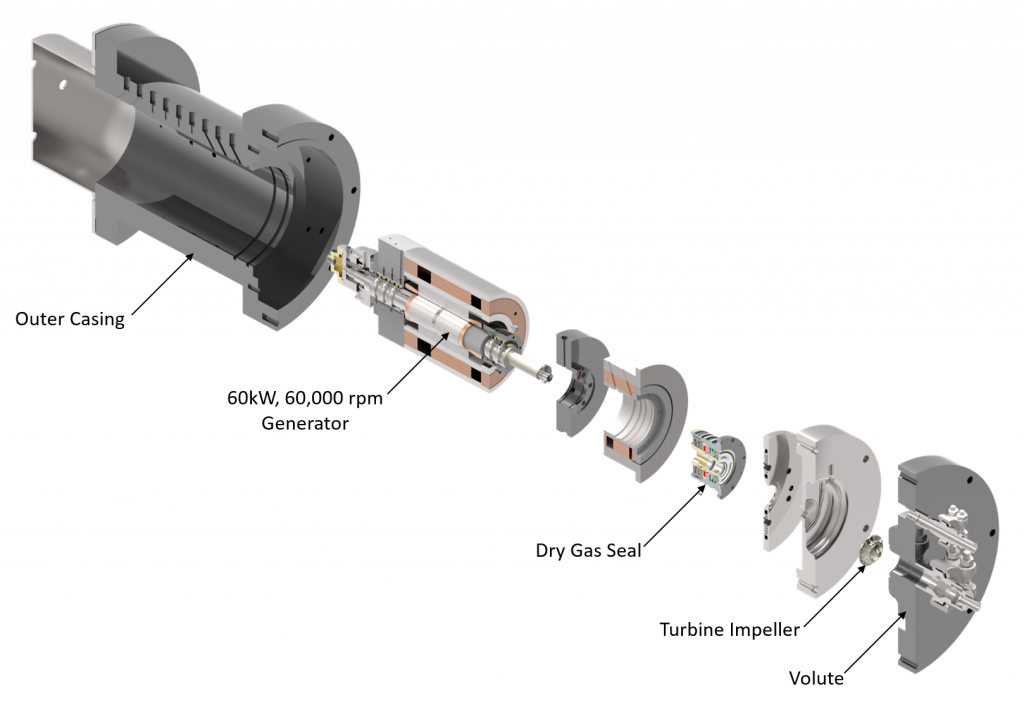
(Image courtesy: Pramod Kumar)
Designing compact turbomachinery – the moving parts involved in energy transfer – comes with a host of challenges, due to the high speeds of rotation ranging from 40,000 to 1,00,000 rpm. To ensure safe and continuous operation, researchers led by Pramod Kumar, Associate Professor, Department of Mechanical Engineering, are working on optimising the dimensions and structure of the components. Some of the components, like impellers, could be as small as a Rs 10 coin. The researchers are also developing Printed Circuit Heat Exchangers (PCHE) which offer very high cooling capacities at higher temperatures and pressures.
There are also other challenges. Due to the extreme conditions in the AUSC power plants, the materials that make up the components need to be strong enough to withstand them over a long time. “The materials can undergo environmental degradation and oxidation due to high temperatures, and corrosion due to steam at that temperature and pressure,” explains Satyam Suwas, Professor and Chair of the Department of Materials Engineering and co-PI of the project. “Additionally, since the components like pipes and turbines are manufactured in parts and welded together, the material should be weldable as well as retain its strength after welding.” Numerous research groups at the NCCCRD are working to develop and validate indigenous materials for these power plants. One such class of materials is a range of nickel superalloys. At high temperatures, most metals may lose their shape and strength, but these superalloys do not.
Researchers like Praveen Kumar, Associate Professor at the Department of Materials Engineering, are also working on understanding how the materials behave. “We plan to simulate the AUSC power plant conditions by conducting experiments at high temperatures to study the structural integrity of the materials – to see if the high pressure and temperature cause any deformations and damage in the material beyond what is permissible,” he explains. All materials may undergo fatigue and other time-dependent deformation processes. This requires regular monitoring to assess the remaining lifespan of the components and to check if the materials need to be replaced. So another aim of his group’s work is to develop predictive models that will let engineers understand how the material will behave over time so that they know when to inspect and replace the parts.
Another core area of research is the development of gasification techniques for solid coal with high ash content. Gasification is the process of converting solid carbon-based fuel into its gaseous form, which is less harmful for the environment than burning solid coal. “While gasification is a well-known technology, it has been used mainly for coal with a low or medium level of ash content. However, the coal in India has 35-40% ash content, which is much higher than that of imported coal and could cause problems in the industrial processes,” says S Dasappa, Professor at the Centre for Sustainable Technologies.
At high temperatures over a long period of time, the ash content in the coal often forms sediments – a process called ash fusion – which can hinder the functioning of machinery. Dasappa explains, “We are using a concept called cyclone gasification, which could help address the issue.”
The researchers are also looking to use products from gasification, like carbon monoxide, hydrogen and methane, to produce hydrogen-rich fuels, methanol and fertilizers.
Gasification also comes into play in reducing carbon emissions by capturing the CO2 generated. “In gasification, we do not allow the entire amount of coal to be converted to combustible gases, which allows us to separate CO2 for possible usage. We can then capture and remove the carbon dioxide from these gaseous species so that the process is greener than a typical coal-driven Integrated Gasification and Combined Cycle (IGCC) power station,” says Dasappa.
Technologies that reduce the environmental footprint of fossil fuels like coal are critical to supplement India’s renewable energy efforts, because as Dutta puts it, “We cannot do away with fossil fuels in the near term.”